NEWS
Making ready-mix concrete at scale with Ready Mix Tees Valley
The brief
Material Evolution conducted a production trial with Ready Mix Tees Valley to demonstrate green concrete being produced at scale, showcasing the first iteration of MevoCem, our ultra-low carbon cement, which offers an up to 85% reduction in carbon emissions to traditional OPC.
Dr. Andrew Longstaff, our senior materials scientist at Material Evolution, helped our team put the material to the test by creating a concrete slab with a leading supplier of ready-mix concrete to Teesside and the surrounding area.
Key findings
- The material was used to create a ready-mix concrete slab with enhanced chemical resistance and higher durability
- The concrete was designed to meet RC50 XF4/PAV2 for heavy duty pavements in accordance with BS8500
- The slab was readily powerfloated to achieve a good quality finish, and the final product showed no surface defects due to bleed or plastic shrinkage upon setting
Our approach
The trial took place over the course of an afternoon, during which Ready Mix Tees Valley produced a 9m2 concrete slab with MevoCem, designed to meet S4 slump class standards.
As a one-part activated solution, using MevoCem did not require Ready Mix Tees Valley to handle of large quantities of chemical activators, they simply replaced the existing binder at the batching plant. There was no need for retooling and no health and safety risks beyond normal handling of OPC.
The team finished the concrete slab with a power float, achieving a smooth and durable surface without any issues related to setting time, surface integrity, or finish quality. Despite being poured on a warm, windy day, the slab showed no bleed or plastic shrinkage cracking. The low heat of hydration and enhanced water holding within the geopolymer gel reduced water mobility and migration.
Beyond the site trial, the product has been tested to the British Standards Institution’s Flex350 V2 EAD 040287-00-0404, a rigorous standard simulating 25 years of UK weathering through freeze and thaw cycles. This confirms its resilience under challenging conditions.
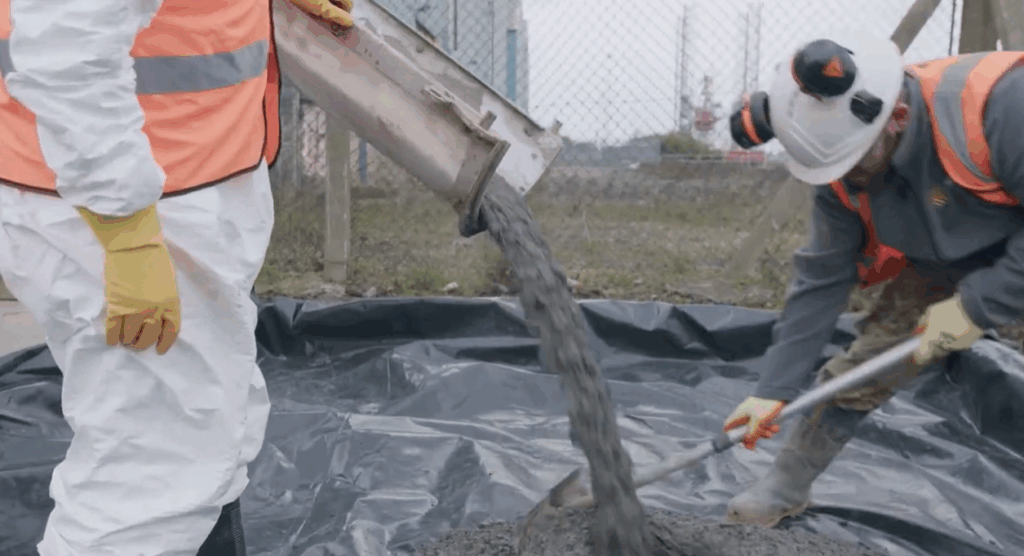
The technology behind MevoCem
MevoCem is produced using proprietary alkali fusion technology that eliminates the need for heat, massively slashing energy consumption during the production of our cement in comparison to traditional OPC. This innovation cuts CO2 emissions to just 144-196 kg of CO2e emitted per tonne – an up to 85% reduction in comparison to traditional cement.
Our alkali fusion process also allows us to use industrial byproducts as the inputs for our cement alternative, as it improves reactivity in otherwise less reactive materials. By transforming industrial byproducts into valuable raw materials, we reduce the need for virgin resources and keep waste out of landfills, thereby promoting a circular economy.
Our expert data team have also developed AI and machine learning tools to predict how these materials will perform in the production of low-carbon cement, which enables our R&D team to adjust ingredients as necessary based on the model’s predictions.
Our eventual goal is to use these techniques to save 1 gigatonne of CO2 by 2040. Find out more about our green credentials here.
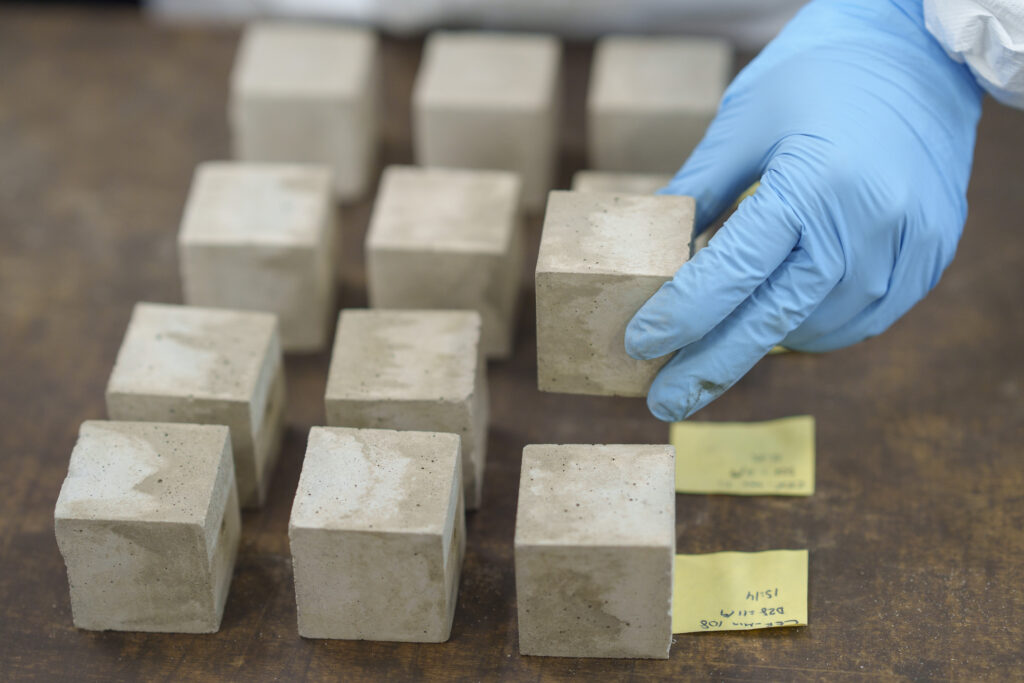
The solution
Since the trial with Ready Mix Tees Valley occurred, the MevoCem formulation has been further refined to improve its performance, leading to the version that’s currently available in the market (and to which the below data corresponds). Compared to traditional binders, MevoCem shows good early strengths, rapid strength development, low heat of hydration and improved durability.
- Strength development
When compared to a CEM III/A, MevoCem offers clear advantages in water-cement ratio. CEM III/A defined under the European cement standard EN 197-1 contains 36-65% ground granulated blast furnace slag (GGBS) blended with Portland cement clinker.
Typically, CEM III/A requires a water-cement ratio of 0.50-0.55 to achieve adequate workability, often resulting in slower strength development. It has compressive strengths of approximately 8-12 MPa at day 1, depending on the mix design and curing conditions, and workability can be limited without the use of chemical admixtures. However, when MevoCem is used at these water-cement ratios, it still achieves good workability and comparable day 1 strengths, but without compromising on ultimate strength.
Fig.3 below highlights the strength development for each powder content at a range of water-cement ratios, where almost all of the samples tested achieved greater than 50 MPa at day 28. It is possible to obtain finished products of C50 strength classification at 400 kg/m3, and 450 kg/m3 powder content with an initial S4 slump, and of C60 strength classification at 450 kg/m3 powder content with an S3 initial slump.
- Effective flowability
MevoCem showed effective flowability even at lower water-cement ratios, ensuring ease of application without the need for admixtures. This reduced water demand also enhanced the material’s microstructure, leading to higher day 1 strengths, and day 28 strengths consistently above 50 MPa. Unlike CEM III/A, which relied on extended curing times for strength gain, MevoCem provides rapid strength development, making it particularly well-suited for precast applications and accelerated construction timelines.
- Low heat of hydration
Using an increased powder content does not incur the disadvantages associated with OPC. The heat of hydration of MevoCem is low, resulting in reduced water loss due to evaporation, and thus eliminating plastic shrinkage. Problems that may occur due to thermal build up associated with pouring large structures are minimised, and thermal cracking is also eliminated.
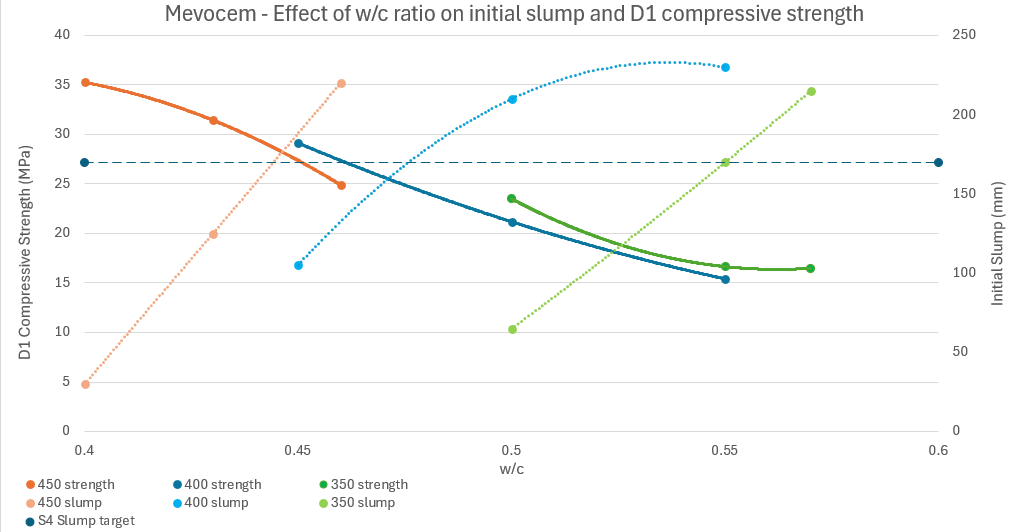
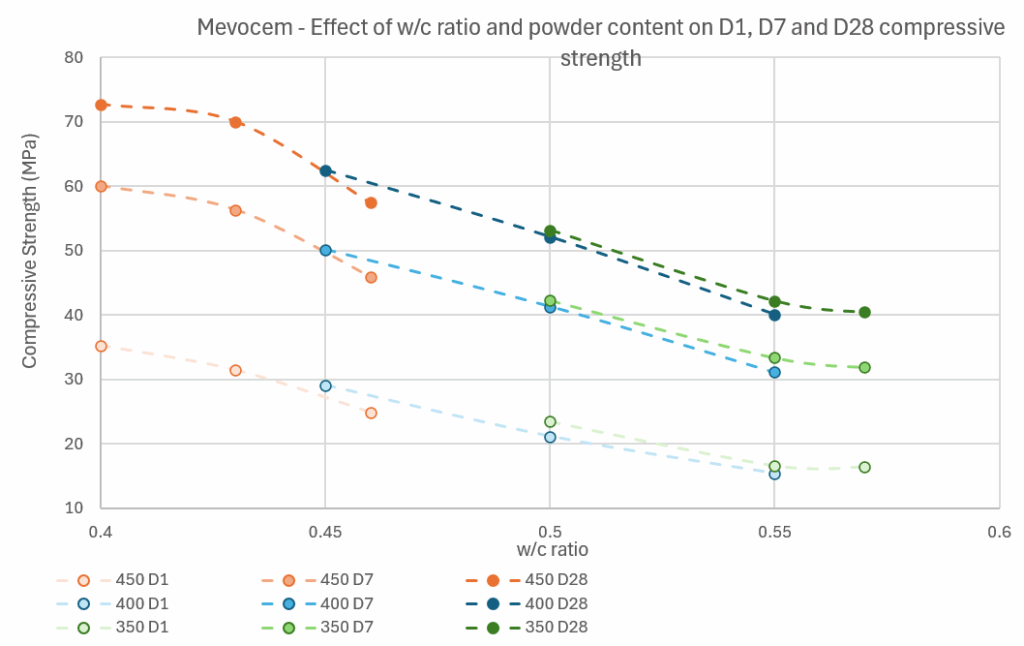
The end result
The trial underscores the practicality and performance of green cement, addressing longstanding concerns around quality and adaptability.
As regulatory pressures mount and industry stakeholders seek credible pathways to reduce embodied carbon, the success of this trial marked a pivotal step toward widespread adoption of low-carbon cement alternatives.
Jim Greenwood, managing director of ReadyMix Tees Valley, said: “We’ve partnered with Material Evolution because we want to take green concrete to the next level – we have our carbon negative aggregate, and now we’re moving into the cement realm, which is Mevo’s area of expertise.
“Green credentials are becoming more and more important to our customers, and we are being asked for greener concrete. Our partnership with Mevo isn’t just good business, it’s purpose.”
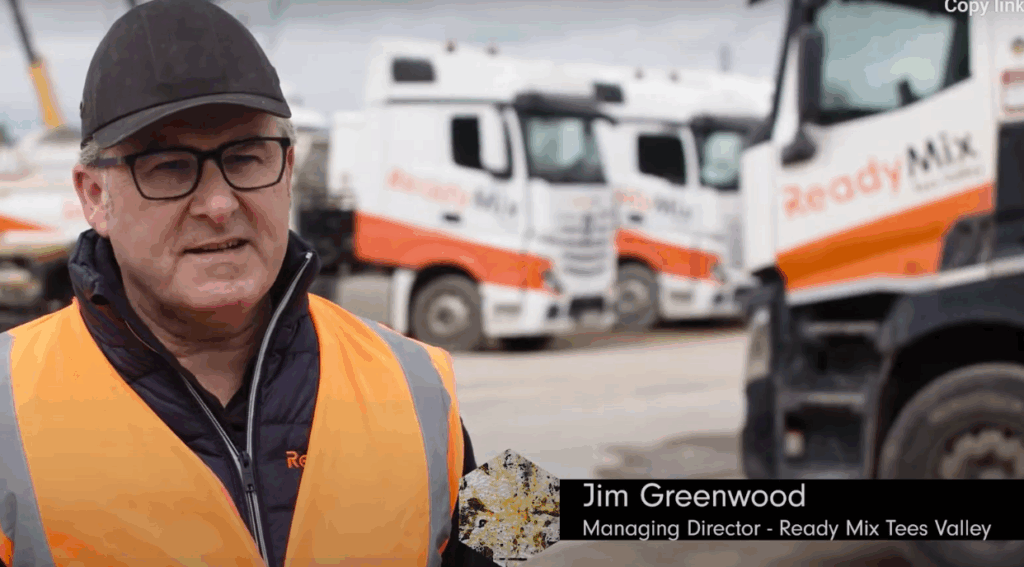
Contact us today to discuss your low-carbon cement solution
MevoCem is just the beginning, with research into a net zero cement product and other bespoke applications well underway at Material Evolution.
Get in touch to find out how we can support your next construction project.